Comprehensive Guide to Excavator Maintenance: Safety, Efficiency, and Environmental Responsibility
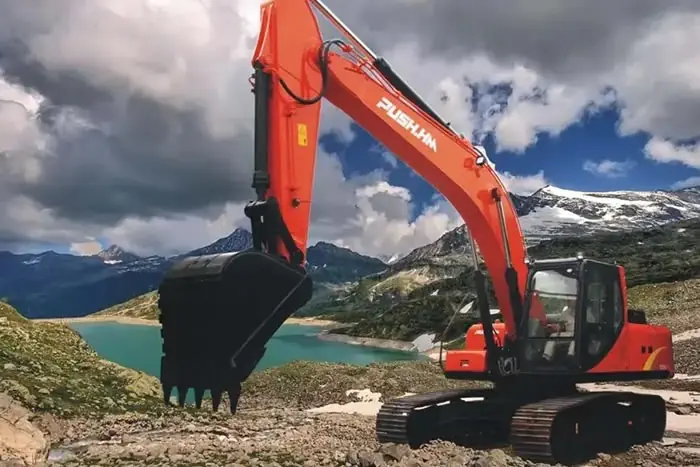
1. Preparation before maintenance
Safety protection preparation
Before starting to repair the excavator, the maintenance personnel must wear appropriate personal protective equipment, including hard hats, safety shoes, protective gloves, etc. These equipment can effectively reduce the risk of accidental injury during the maintenance process. For example, hard hats can prevent the head from being hit by parts falling from high places, and safety shoes can prevent the feet from being crushed by heavy objects.
Site preparation
Make sure the maintenance site is flat, solid and has enough space. If the site is uneven, it may cause the excavator to move unexpectedly during the maintenance process, causing casualties and equipment damage. At the same time, clear the debris and obstacles around the maintenance site to maintain a good working environment.
Tool and equipment preparation
Prepare and check all kinds of tools and equipment required for maintenance, such as wrenches, screwdrivers, jacks, cranes, etc. Make sure the tools are intact and the accuracy is up to standard. For power tools, check whether the wires are damaged and whether the insulation performance is good. The right tools are the key to safe and efficient maintenance.
Data preparation
Collect the excavator's operating manual, maintenance manual, circuit diagram and other relevant information. These materials can provide maintenance personnel with detailed parameters, structural information and maintenance steps of the equipment, which is helpful for accurately judging faults and performing maintenance operations.
2. Points to note during maintenance
Precautions for engine maintenance
Fuel system
When repairing the fuel system, first release the pressure in the fuel system to prevent fuel from spraying out and injuring people. When disassembling components such as fuel injectors, pay attention to protecting their precision structures to avoid collisions and damage. When cleaning the fuel filter, use a clean solvent and install it in accordance with the prescribed method to prevent impurities from entering the fuel system.
Lubrication system
When changing the engine oil, make sure the engine is in a warm state so that the oil can be discharged more smoothly. At the same time, use engine oil that meets the requirements of the excavator. When adding engine oil, pay attention to the oil level not being too high or too low. Too high may cause problems such as increased engine running resistance and oil seal leakage. Too low will not provide sufficient lubrication.
Cooling system
When repairing the cooling system, pay attention to the selection of coolant. Different types of Excavators may have different requirements for coolant. Use appropriate coolant and avoid using ordinary water, as ordinary water may cause corrosion and scaling. When checking the Radiator and water pipes, check for leaks and blockages, and repair or replace any problems found in a timely manner.
Precautions for hydraulic system maintenance
Pressure release
Before repairing the hydraulic system, the pressure in the system must be released. This can be achieved by operating the corresponding valve or using a special pressure release tool. Otherwise, high-pressure hydraulic oil may suddenly spray out and cause serious harm to the maintenance personnel.
Cleaning work
The hydraulic system has extremely high requirements for cleanliness. When disassembling hydraulic components, it should be done in a clean, dust-free environment. Use clean containers to store the disassembled hydraulic components and hydraulic oil to prevent impurities from entering the system. Before installing new hydraulic components, they should be thoroughly cleaned and inspected.
Seal processing
When replacing seals in the hydraulic system, use original factory-matched seals. When installing seals, pay attention to the correctness of their installation direction and position to avoid hydraulic oil leakage due to poor sealing. At the same time, avoid damage to the seals during installation.
Electrical system maintenance precautions
Power-off operation
When repairing the electrical system, first disconnect the power supply, including the main power supply and the negative pole of the battery. This can prevent electric shock accidents. During the operation, use insulating tools to avoid direct contact with electrical connectors and wires with your hands.
Line inspection
When checking the electrical circuit, check whether the wires are damaged, aged, short-circuited, etc. For any problems found, use appropriate wires to repair or replace them. When connecting the wires, ensure that the connectors are firm, the contact is good, and the insulation is done well.
Electrical component testing
When testing electrical components (such as sensors, controllers, etc.), use professional testing equipment and follow the correct testing methods. Avoid using improper testing methods to damage electrical components. For faulty electrical components, replace the original accessories in time.
3. Inspection and testing after maintenance
Overall appearance inspection
After the maintenance is completed, check the overall appearance of the excavator to ensure that all components have been properly installed and there are no missing tools or parts on the equipment. Check whether the protective devices of the equipment are installed in place, such as guards, railings, etc.
Functional test
Startup test
Start the excavator and check whether the engine starts smoothly and whether there is any abnormal noise, vibration or smoke. Observe the indicator lights on the dashboard to ensure that the operating status of each system is normal.
Action test
Operate the various working devices of the excavator, such as the boom, dipper, bucket, etc., to check whether their movements are flexible and accurate, and whether there is any jamming or abnormal noise. At the same time, check whether the pressure of the hydraulic system is normal, and test the performance of the hydraulic system under different working conditions by operating different actions.
Electrical system test
Check whether the lighting system, horn, instrument and other electrical equipment of the excavator are working properly. Test the functions of various sensors, such as liquid level sensors, pressure sensors, etc., to ensure that they can accurately transmit signals to the controller.
4. Environmental protection precautions
Waste oil treatment
Waste oil, hydraulic oil, etc. generated during maintenance should be properly collected and not dumped at will. These waste oils should be stored in special waste oil containers and handed over to qualified recycling and treatment agencies for treatment in accordance with environmental protection regulations.
Waste parts treatment
Replaced waste parts, such as metal parts, rubber seals, etc., should be stored in a classified manner. Recyclable parts should be recycled reasonably, and non-recyclable parts should be treated in accordance with environmental protection requirements to avoid pollution to the environment.
Why Choose SAIVS™ as Your Supplier?
Committed to innovation and customer needs, SAIVS specializes in high-quality machinery components for diverse industries like construction, mining, and agriculture. They offer a wide range of parts, including undercarriage components for popular brands, ensuring optimal performance and durability. values customer satisfaction, providing competitive prices, fast shipping, and exceptional service to keep your operations running smoothly.