Mini Excavator Maintenance: Make Your Work Easier
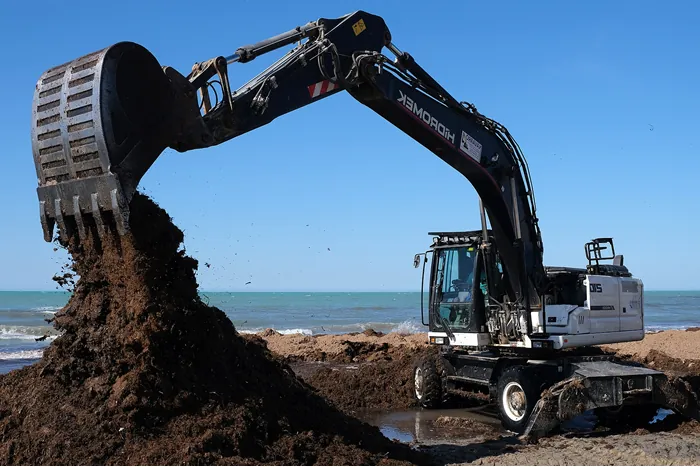
Mini excavators, the workhorses of compact construction, require consistent care to operate at their best.
Regular maintenance not only extends the lifespan of these machines but also prevents costly repairs and ensures operator safety.
This guide outlines 14 essential tips for keeping your Mini Excavator fleet in top condition.
1. Invest in Operator Training
An effective preventative maintenance program starts with well-trained operators.
Operators who understand normal operating conditions are better equipped to identify potential problems during daily use.
Training should cover engine and exhaust issues, loose bolts, worn belts, missing parts, and filter replacements.
Recognizing these red flags allows for early intervention and prevents minor issues from snowballing into major repairs.
2. Follow a Scheduled Maintenance Approach
Refer to your mini excavator's maintenance manual to create a customized service schedule.
This manual details recommended service intervals for everything from fluid levels to track tension.
Here's a general breakdown for a well-rounded maintenance routine:
Daily: Operators should check fluid levels, inspect connections, and ensure attachments are well-greased.
Weekly: Grease the slew-ring bearing and check track tension and drive belts.
Biannually: Schedule professional preventative maintenance to ensure a thorough inspection by certified technicians.
Every Two Years: Perform more time-consuming maintenance tasks, such as cleaning fuel injectors.
3. Conduct Daily Pre-Operation Walkarounds
A quick daily walkaround reduces the risk of overlooking critical issues.
Start by checking the hydraulic cylinders, the lifeblood of the attachment system. Inspect the rods, seals, and linkage for signs of damage or wear.
4. Inspect Attachments and Couplers
Loose or damaged attachments pose safety hazards and can strain the excavator's arm.
Regularly check the attachment and coupler for any signs of rust, cracks, or excessive wear.
Replace worn components to maintain optimal performance and prevent unnecessary stress on the excavator's arm.
5. Open the Hood and Inspect Internal Components
Open the side hood and examine the hydraulic tank, tubes, hoses, plugs, fittings, and connecting joints.
Look for leaks, cracks, or loose connections. Address any issues promptly to prevent fluid loss and potential damage.
6. Monitor Fuel Water Separator
Water contamination in fuel can lead to engine problems. Check the fuel water separator for any water accumulation.
Most models have a clear bowl with a red ring that floats if water is present.
Early detection of water contamination prevents costly repairs to the fuel filter and engine.
7. Maintain the Cooling System
Inspect the cooling system for leaks, faulty hoses, and debris buildup. Clean the system and address any leaks.
Maintain proper coolant levels according to the manufacturer's recommendations.
8. Prioritize Greasing Pivot Points
Daily greasing of the arm, bucket, and other pivot points is a cost-effective way to ensure smooth operation and prevent premature wear and tear on the pins.
9. Examine the Engine Compartment
Remove debris from the engine compartment, tighten the oil cap if necessary, and inspect all engine attachment belts.
Replace any frayed, worn, or broken belts to maintain optimal engine performance.
10. Check Fluid Levels
Engine and hydraulic oil should always be at the recommended levels as specified in the manufacturer's manual.
Operating the excavator with insufficient fluids can lead to severe damage.
11. Maintain Air Filters
Air filters should be checked regularly, especially in dusty environments.
Clogged air filters restrict airflow, reducing engine performance. Replace air filters according to the maintenance schedule or more frequently if necessary.
12. Inspect Tracks and Maintain Proper Tension
Regularly inspect the tracks for rocks, debris, and excessive wear. Remove debris and replace excessively worn tracks.
It's crucial to maintain proper track tension to prevent unnecessary wear and downtime.
Operators working on rough terrain may need to check track tension daily.
13. Ensure Operator Cabin Safety
Inspect the falling object protective structure (FOPS) for loose bolts and tighten them if necessary.
Remove debris from the cabin floor and check for broken switches, controls, or cracked mirrors.
Replace any faulty components to ensure operator safety. Clean windows in enclosed cabs for optimal visibility.
14. Leverage Telematics for Smart Maintenance
Telematics systems provide real-time data on machine health and performance, alerting operators to potential issues and recording maintenance history.
This allows for proactive maintenance and prevents minor problems from escalating into major ones.
With telematics, operators can avoid overlooking critical maintenance needs, saving time and money.
By following these 14 tips and adhering to a manufacturer-recommended maintenance schedule,
you can ensure your mini excavator fleet operates at peak performance for years to come.
Remember, consistent care is vital for maximizing the lifespan and productivity of your mini Excavators.
Why Choose SAIVS™ as Your Supplier?
Committed to innovation and customer needs, SAIVS specializes in high-quality machinery components for diverse industries like construction, mining, and agriculture. They offer a wide range of parts, including undercarriage components for popular brands, ensuring optimal performance and durability. values customer satisfaction, providing competitive prices, fast shipping, and exceptional service to keep your operations running smoothly.